The future of composites in electric vehicles (EV) will likely play a crucial role in shaping the automotive industry. Composites are materials made from two or more materials with significantly different properties; this combination creates a material with enhanced attributes. In terms of electric vehicles, composites provide a promising solution to reduce the weight of vehicles with heavy battery packs and minimise energy consumption.
Table of Contents

Our Future: New Zero-Emission Cars by 2035
The role of composites in electric vehicles is evolving rapidly as the automotive industry adopts a greener approach to a low-carbon economy. It has recently been announced that ‘the government’s ban on the sale of new petrol and diesel cars will come into effect from 2035.’ Those buying new cars will no longer be able to buy petrol or diesel vehicles; instead, they will have to purchase a zero-emission vehicle. Hence, the role of composites in electric vehicles is undergoing rapid development at this time.
The Weight Reduction Revolution: Advanced Composites in EVs
One of the main reasons for using composites in electric vehicles is that they are lightweight. Lightweight materials are crucial because EV batteries often weigh 15-20% more than gas-powered engines. The weight of a car directly impacts its energy efficiency, acceleration time, ease of handling and overall performance. Therefore, advanced composites are beneficial materials when it comes to manufacturing high-performing, energy-efficient EVs.

Carbon Fibre Reinforcements
Carbon fibre composites, often in the form of carbon fibre-reinforced polymers (CFRP), offer several advantages in terms of strength, weight and design flexibility. This material is known for its strength-to-weight ratio, and when used in manufacturing EVs it provides a lightweight solution that maintains strength and integrity. Carbon fibre reinforcements are commonly used to create the chassis of an electric vehicle, as well as in frames and body panels. Its flexibility also assists in making a vehicle aerodynamic, as exterior panels can be designed to minimise air resistance. This enhances energy efficiency and allows for a longer driving range.
Fibreglass Composites
Fibreglass composites, which usually consist of glass fibres and polyester resin, are also used in various parts of an electric vehicle. This includes manufacturing low-weight, high-strength body panels, hoods and doors, often with lower costs than carbon fibre. This composite can also be used in interior components such as seats, panels and trims, which reduces the overall weight of a car and improves performance. It can also be used to insulate batteries and electronic components, which is essential for maintaining battery efficiency and lifespan
Impact on Vehicle Performance
When it comes to strength, carbon fibre is renowned for its high tensile strength, making it stronger than steel and allows for the construction of lightweight yet incredibly strong components. Fibreglass is not as strong as carbon fibre and is more commonly used in areas that only need moderate strength.
Carbon fibre is a high-performance material with a higher cost; the manufacturing process and raw materials make it more expensive than fibreglass.
Using these composites in the manufacturing process of electric vehicles significantly impacts a vehicle’s weight, battery efficiency and range, aerodynamic design, structural integrity, corrosion resistance, acceleration, ease of handling and overall performance.
Enhanced Energy Efficiency: Composite Materials in Electric Vehicle Design
Composites enhance energy efficiency in multiple ways through weight reduction, battery efficiency, improved braking and acceleration, aerodynamic designs, thermal management for batteries, and allowing for extended driving ranges. Composites can improve aerodynamic designs, thermal management systems and battery efficiency, as these significantly impact the energy efficiency of a vehicle.
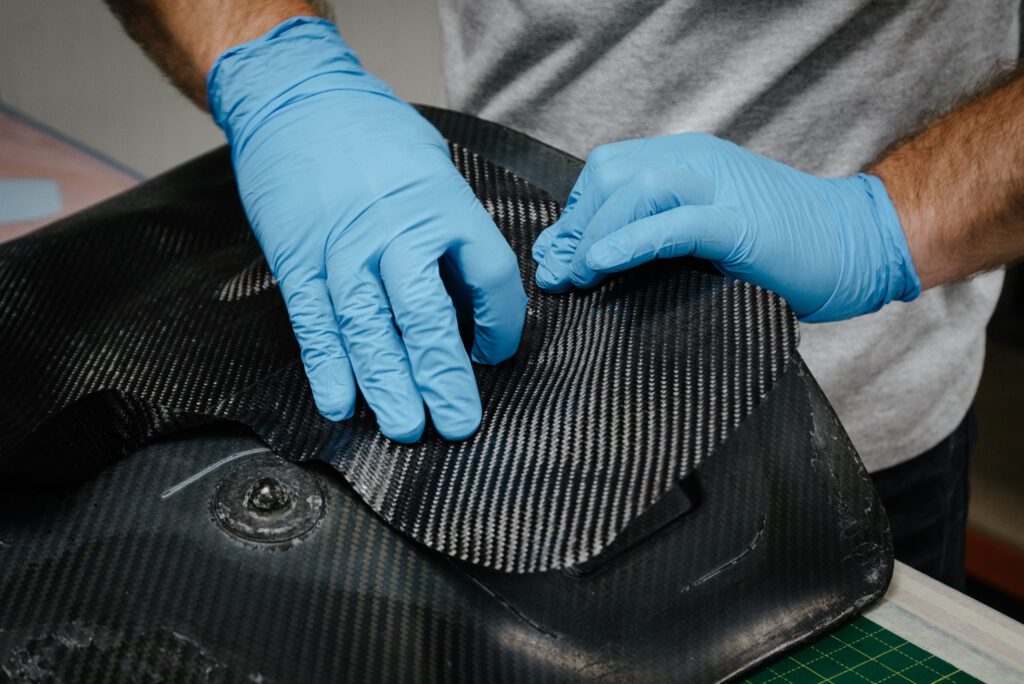
Improving Aerodynamics with Composites
Composite materials allow for more aerodynamic shapes, particularly when used in designing body panels and other exterior components. Improved aerodynamics reduces air resistance and enhances the efficiency of the vehicle at higher speeds; it minimises drag and contributes to better energy efficiency, which contributes to a longer driving range.
Thermal Management Systems
Composite materials can be engineered to have specific thermal properties. This plays an important role in EVs as batteries need to be maintained at an optimum operating temperature. Carbon fibre has thermal conductor properties, which are effective at maintaining temperatures; it can also dissipate heat, which contributes to the efficiency of vehicles. Fibreglass is an effective thermal insulator and can help regulate the temperature of batteries and other electronic components when used as a layer of insulation.
Battery Efficiency and Cooling
Battery efficiency and cooling directly impact the performance, lifespan, and safety of the vehicle’s battery system. Thermal management ensures the batteries operate within optimal temperature ranges. Electric cars are equipped with heating and cooling systems which regulate the temperature of the battery pack. This ensures optimal performance and prevents batteries from overheating or degrading due to temperature. A consistent battery temperature also allows for reliable power delivery and optimal energy storage, contributing to a more efficient driving experience.
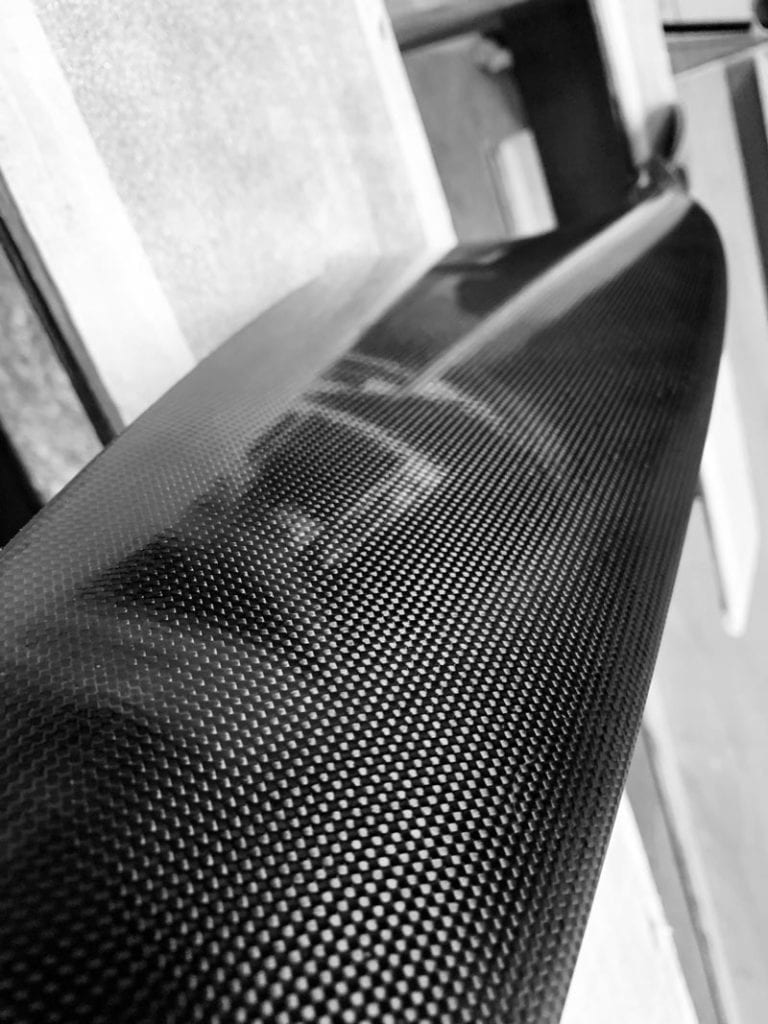
Extending the Range: Composite Battery Technologies
Advancements in battery technology, along with the use of composite materials, contribute to extending the range of electric vehicles (EVs). This can be done through lightweight battery casings, composite anode and cathode materials, and battery packaging. Let’s take a look at how the integration of composites and advancements in battery technology contribute to increasing the range of EVs.
Composite Anode and Cathode Materials
A battery has two electrodes which facilitate the flow of electronic charge. The anode electrode is the negative charge and the cathode electrode is the positive. During the charging process, electrons flow from the cathode to the anode, storing energy that can later be used. Composite materials can be used for the anode and cathode to advance the performance and efficiency of batteries used in electric vehicles (EVs). These composites are designed to address challenges such as energy density, cycling stability, and overall battery longevity.
Innovations in Battery Packaging & Casings
There are various innovations in battery packaging, from the physical design to the materials used in its manufacture. For example, some electric vehicles incorporate the battery pack as a structural element of the vehicle chassis.
Lightweight composite materials, such as carbon fibre-reinforced polymers (CFRPs), can be used in the construction of battery casings. Lightweight composites help reduce the overall weight of the battery pack, contributing to improved energy efficiency and extended range. Therefore, it is important that battery casings are produced using lightweight materials to increase the range of a vehicle.
Safety and Durability: The Role of Composites in EV Structural Integrity
Composites play a significant role in enhancing the safety and durability of electric vehicles (EVs) by contributing to the structural integrity of various components. One example includes a composite material’s ability to absorb and dissipate energy from an impact more effectively than traditional materials, such as steel. Composite materials also enhance other factors, such as fire resistance. Manufacturers can enhance collision safety, protect passengers, resist corrosion and improve safety features by using composite materials in electric vehicles.
Crash Safety and Composite Structures
Composites, especially carbon fibre-reinforced polymers, have high strength-to-weight ratios. These types of materials can absorb and dissipate energy, as well as distribute energy; this minimises the force that passengers experience during a crash, reducing the risk of injuries. Composites also provide protection when used for components such as the chassis and body of a car, as these materials maintain structural integrity.
Durability Testing and Longevity
Durability testing aims to simulate the effects of different environmental conditions, the way a vehicle is used and mechanical stresses that may occur in its lifetime. This is especially important in electric vehicles as two aspects must be tested: the traditional vehicle components and the electric and energy storage systems. This may include cyclic tests of charging and discharging batteries, fast charging tests, simulating road conditions, simulating heavy rain and the safety of electronics, recyclability testing and more. These types of tests are an ongoing process and may change as consumers develop different usage patterns and as technology advances.
Fire-Resistant Composite Solutions
Fire resistance composites protect valuable components such as the battery pack and mitigate the risks of fire-related incidents in electric cars. Solutions include fire-resistant casings, thermal barriers, fire-resistant chassis and body frames, wiring coated in protective sheathing, materials that have fire suppression properties, smart battery systems that detect early temperature changes and using materials that effectively dissipate heat.
Advanced Composites in Electric Vehicle Interiors
Advanced composites have many benefits when it comes to electric vehicles, especially as manufacturers begin to focus on creating environmentally friendly, zero-emission vehicles. Not only do these materials offer a reduction in weight, design flexibility and improved durability, but they also enhance sustainability. Let’s take a look at how manufacturers can produce lightweight, stylish interiors that use sustainable materials.
Lightweight and Interiors
Composites can be used to design lightweight, stylish interiors, and there is a balance between aesthetics, material choices, costs and function. For example, carbon fibre may be used as a robust, lightweight material for a seat frame; however, there may be larger costs involved than when using materials such as lightweight alloys. Advanced composites also give designers greater flexibility to create complex shapes that are not possible with traditional materials. This allows manufacturers to create modern, innovative designs that are aerodynamic and optimise aesthetics and functionality.
Noise Reduction and Comfort
Advanced composites can be used strategically to reduce noise and increase levels of comfort. Some composites have sound-absorbing properties, whilst others have dampening properties. These materials can be used in the interior panels of EVs to reduce levels of noise related to the road, wind or mechanical elements and reduce vibrations. Some composites can provide dual-action with sound-absorbing and thermal properties; these can be incorporated into multiple parts of the vehicle as a barrier against noise and changing temperatures.
An example of this would be composite materials being used in laminated glass for windshields to reduce wind noise and improve insulation. These types of materials may also be used in wheel arch linings to dampen noise from tyres – especially noticeable in zero-emission vehicles that are quieter than traditional engine-based vehicles.
Environmental Benefits: Energy Savings and Emission Reduction
Energy savings can be achieved within the manufacturing process itself, as lightweight composite materials often require less energy to produce than traditional materials. This contributes to a lower carbon footprint in the manufacturing stage.

A company may also implement closed-loop manufacturing when using sustainable composites, in which waste materials are recycled within the production cycle. This further reduces the environmental impact and creates a more sustainable process when manufacturing EVs.
One of the most difficult tasks is reducing the weight of vehicles in order to minimize energy consumption, according to an article titled ‘Composites for electric vehicles and automotive sector: A review.’ A lighter vehicle requires less energy to operate and by using composites instead of traditional materials, energy efficiency and driving ranges can be improved. Lightweighting also decreases energy consumption per mile, which supports emission reduction.
Tesla: Successful Integration of Composites in Electric Vehicles
There are many success stories of integrating composites in battery electric vehicles, plug-in hybrid electric vehicles, and fuel-cell electric vehicles. In June 2023, the largest EV manufacturers included BYD (China), Tesla Inc (United States) and VW Group (Germany).
The Tesla Roadster uses lightweight carbon fibre and an epoxy composite for its skin, which makes it highly aerodynamic. According to Tesla, this composite ‘took two years to design, prototype, test, redesign and retest.’ It also uses carbon fibre body panels layered with glass, polypropylene, carbon and epoxy resin. Tesla’s Cybertruck uses ‘Ultra-Hard 30X Cold-Rolled Stainless-steel’ for its exterior shell and polymer-layered composite for its ‘Armour Glass’ feature, which absorbs and redistributes energy from an impact.
Driving Forward with Advanced Composites in Electric Vehicles
The future of sustainable composite materials in electric vehicles is promising, focusing on lightweight, high strength-to-weight ratio composites that improve performance and vehicle safety whilst reducing carbon footprint. It is likely that advanced composite materials such as carbon fibre-reinforced polymers (CFRP) will become more widely used and that manufacturers will continue to develop composites with enhanced strength and durability.
As technology advances, it is expected that the cost of composite materials will decrease as innovative manufacturing processes such as automated fibre placement and 3D printing become more widely available. This will enable manufacturers to produce electric vehicles that are more cost-effective on a larger scale, as well as integrate composites into the finer details of vehicles, such as battery enclosures and thermal management systems.
