CNC machines manufacture parts for a wide range of applications. In this post, we will explore the application of CNC machines across six different sectors. This includes the aerospace, automotive, renewable energy, marine, medical, and defence industries.
At Piran Composites, we specialise in large-scale, five-axis CNC machining and work on world leading projects in a variety of industries. So, let’s begin with a short introduction to CNC machines, followed by a breakdown of industry examples.
Table of Contents
Introduction to CNC Machines
CNC machines automate the cutting, shaping, drilling, and finishing of materials like metal, wood, plastic, and composites. They are controlled by computer programs, allowing for high precision and efficiency in manufacturing parts. Computer Numerical Control (CNC) technology supports complex designs, reduces manual labour, and enhances productivity and quality in production processes.

The Intersection of CNC Machining and Composite Materials
The intersection of CNC machining and composite materials marks a significant advancement in manufacturing technology. By combining CNC’s precision and efficiency with the lightweight, durable properties of composite materials, manufacturers are able to produce complex parts with supreme accuracy and strength. This enhances product performance and optimises production processes.
Revolutionising Manufacturing Across Industries
Advanced manufacturing technologies, such as CNC machining, are revolutionising industries – not only by enhancing performance and efficiency but also by reducing waste. This supports companies to streamline production, open new avenues for design and functionality and move towards more sustainable manufacturing methods.
Precision Engineering in Aerospace Components
CNC machining is used to manufacture precision aerospace components, including:
- Engine turbine blades
- Fittings and fastenings
- Landing gear components
- Fuel bodies
- Avionic enclosures
- Cockpit instrumentation
When manufactured using composite materials, these components enhance the safety, efficiency, and performance of aerospace vehicles and can withstand extreme conditions.
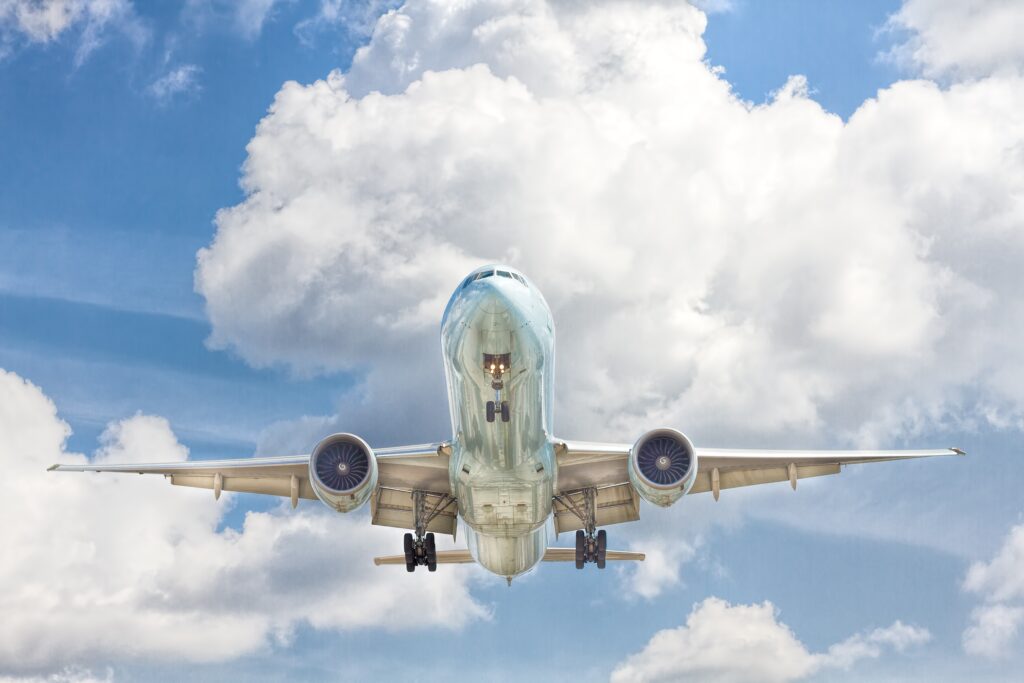
Fabrication of Structural Aerospace Components
CNC machines also manufacture structural aerospace components such as airframe sections and wing spars. This enables the creation of components with exceptional precision and strength and supports the structural integrity of aerospace vehicles.
Custom Tooling and Fixtures for Aerospace
CNC technology also enables the manufacture of custom tooling and fixtures to meet certain specifications and tolerances in the aerospace industry. Typically, CNC milling machines are used to manufacture parts with tight tolerances. This is useful for components such as jet engine turbine blades, which require precise dimensions and shapes, tight tolerances, and must withstand high temperatures and rotational forces.
Automotive Innovations with CNC Machining
CNC machining is used to manufacture automotive components, including:
- Engine blocks
- Gearbox cases
- Exhaust parts
- Suspension components
- Brake rotors
- Wheel hubs
- Steering gears
- Valve bodies
When combined with composite materials, such as carbon fibre, CNC machining can manufacture high-strength-to-weight parts, such as carbon fibre drive shafts. This ensures safety, performance and reliability in automotive vehicles.
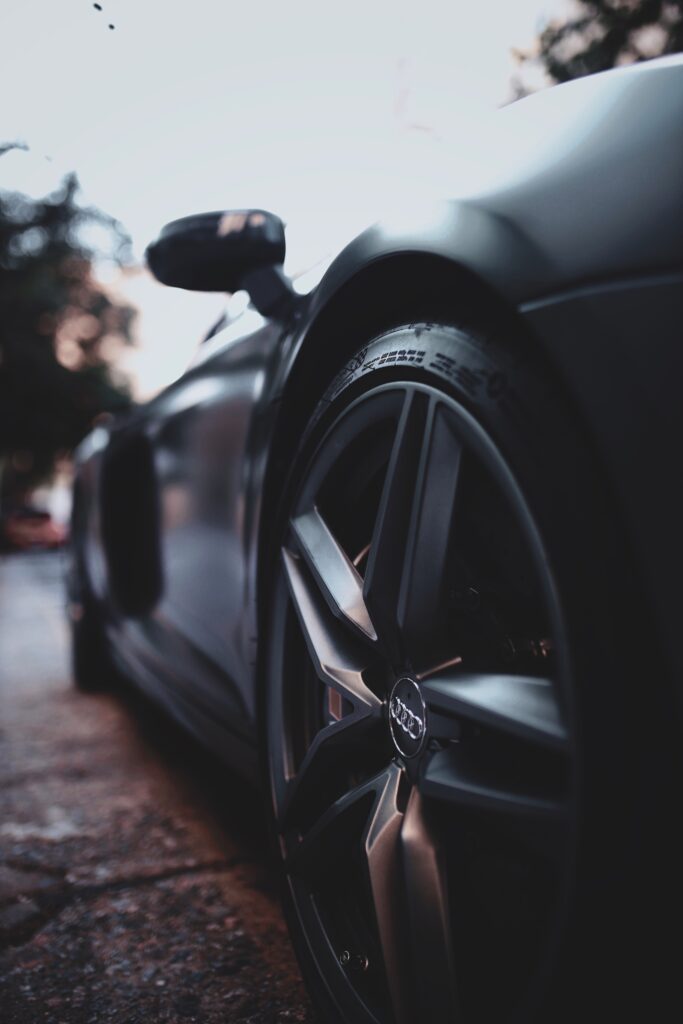
Prototyping and Production of Automotive Parts
CNC machining offers the option for precise prototyping, development and testing of innovative designs. This optimises part performance and ensures compatibility before mass production. An example includes the NP01-EVO prototype race car. This vehicle features a composite body with replaceable sections to reduce repair costs; it aims to create the world’s most affordable closed-cockpit race car with top-level performance.
Composite Materials in High-Performance Vehicles
Composite materials are being increasingly integrated into high-performance vehicles. Advanced materials such as carbon fibre-reinforced polymers, amarid, zylon, and epoxy resins are being used in Formula 1 racing innovations and the latest electric vehicles. These materials provide exceptional strength and lightweight properties, which enhance performance and fuel efficiency. Due to their aerodynamic properties, these types of composites improve handling and allow vehicles to reach higher speeds. These properties are further enhanced with the precision and efficiency of CNC machining.
However, not all CNC machines are suitable for manufacturing with composite materials. For example, electrical discharge machining (EDM) is generally not suitable for composite machining. CNC machines that are compatible with composite materials include milling machines, turning machines, router machines, laser cutters, and 3D printing machines.
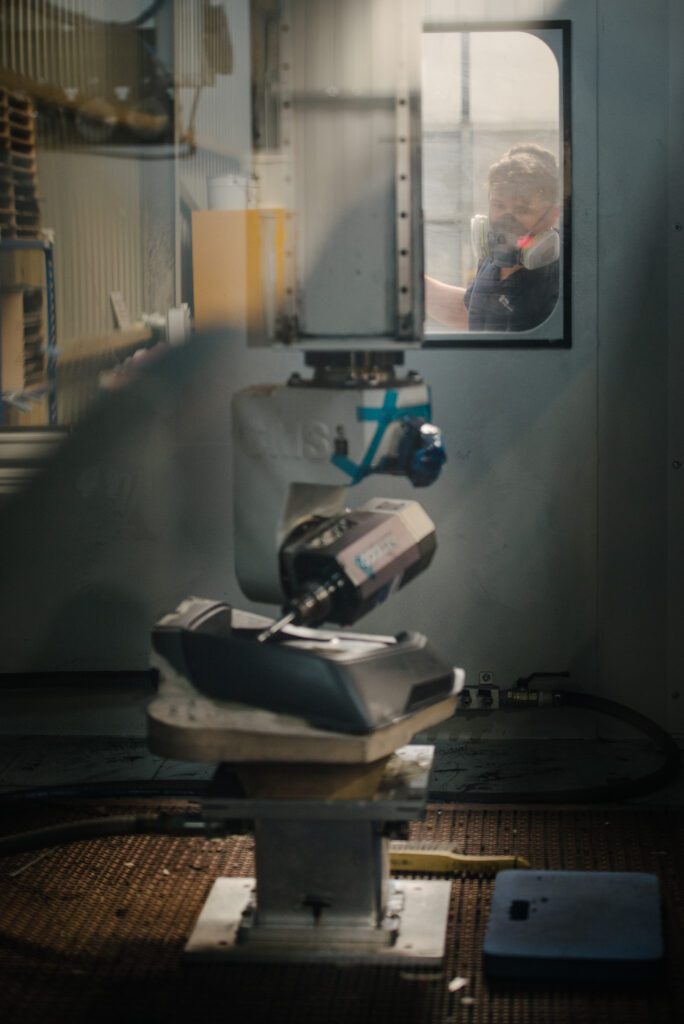
Advancements in Renewable Energy Sector
CNC machining is used to manufacture the following composite components in the renewable energy sector:
- Wind turbine blades
- Hydroelectric turbine components (runner blades, guide vanes)
- Solar panel frames
- Wave energy converter components
- Blades for biomass shredders
CNC machining offers precise shaping for these components with tight tolerances, and composite materials ensure aerodynamic efficiency and longevity. Composites also support components to withstand harsh environments, such as wave energy converter components in the marine environment.
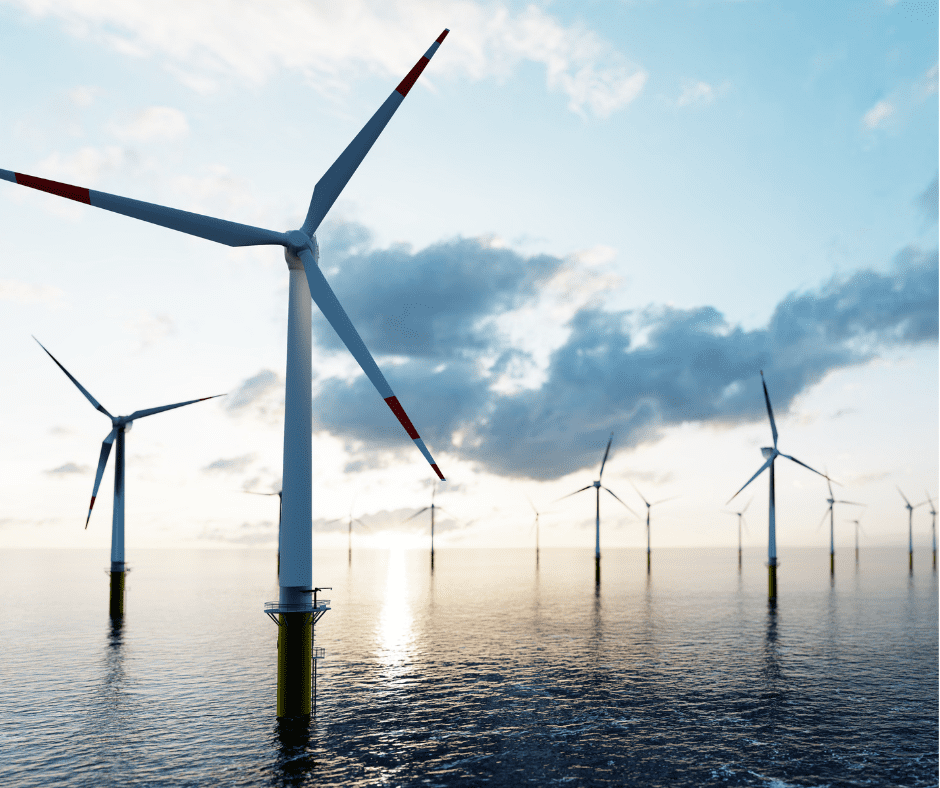
Wind Turbine Blade Manufacturing
Wind turbine blades are manufactured from composite materials such as fibreglass or carbon-fibre-reinforced polymers (CFRP). CNC machining is used to precisely shape and finish these composite blades and ensure aerodynamic efficiency and optimal energy generation. This type of machining also allows for rapid prototyping and enables easy modifications to rotor blades and turbine gear systems.
Components for Solar Energy Systems
Solar energy system components manufactured using CNC machining include solar panel frames, mounting brackets, solar tracking systems, junction boxes, and racking systems. Composites such as fibreglass-reinforced plastics (FRP), carbon fibre-reinforced polymers (CFRP), epoxy resins, polyester resins, and polyethylene terephthalate (PET) film are often used and contribute to the efficiency, reliability, and longevity of solar energy systems.
Marine Industry Applications
CNC machining is used to manufacture the below composite parts in the marine industry:
- Boat hulls
- Deck structures
- Rudders and keels
- Mast and rigging components
- Propellers and shafts
Utilising composite materials and CNC machining technology enables marine manufacturers to produce lightweight, durable, and high-performance components that withstand harsh marine environments.
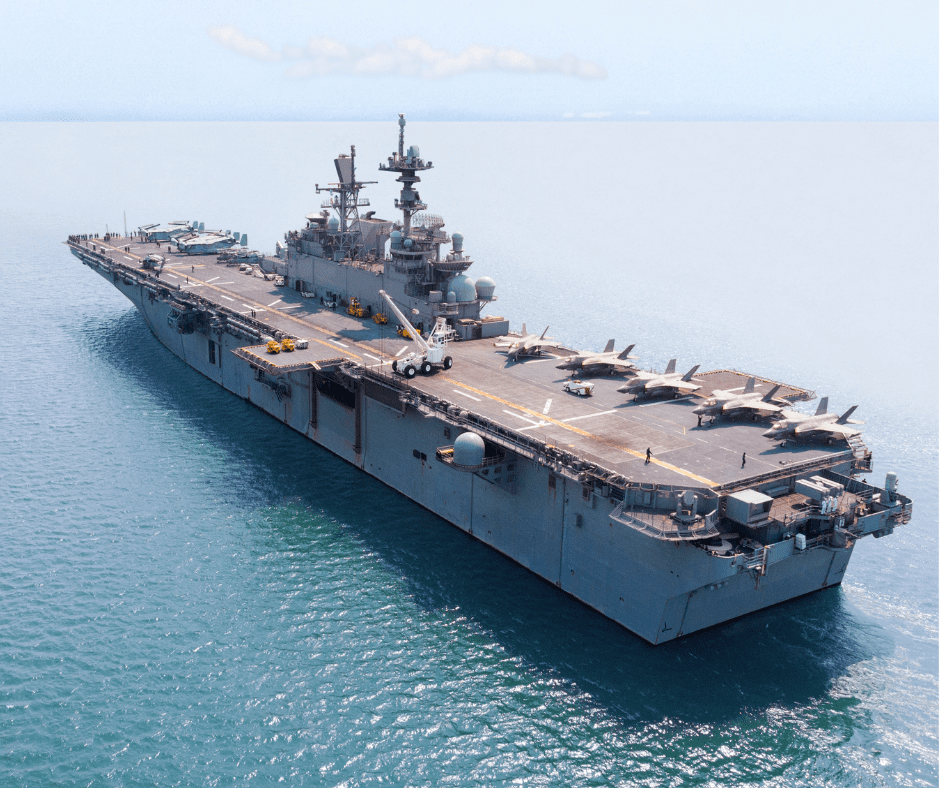
Building High-Strength, Lightweight Boat Hulls
Boat hulls are often crafted from fibreglass or carbon-fibre-reinforce polymers (CFRP) to achieve optimal strength-to-weight ratios and corrosion resistance. CNC machining ensures smooth hydrodynamic performance and can also be used to manufacture boat hull moulds using 5-axis CNC machining.
Custom Parts and Repair
CNC machining also enables precise fabrication and replacement of parts. This is useful when addressing structural damage, optimising performance and customising hull designs. Repair services use advanced composite materials and techniques to restore hull integrity and durability and extend the lifespan of vessels.
Medical Devices and Prosthetics
Another industry that uses CNC is the medical industry. CNC machines can be used to manufacture the following medical components:
- Orthopaedic implants
- Dental prosthetics
- Cranial implants
- Prosthetic limbs
- External fixation devices
The use of CNC machining and composites produce precise medical devices and prosthetics that enable proper fit and alignment with biocompatible materials.
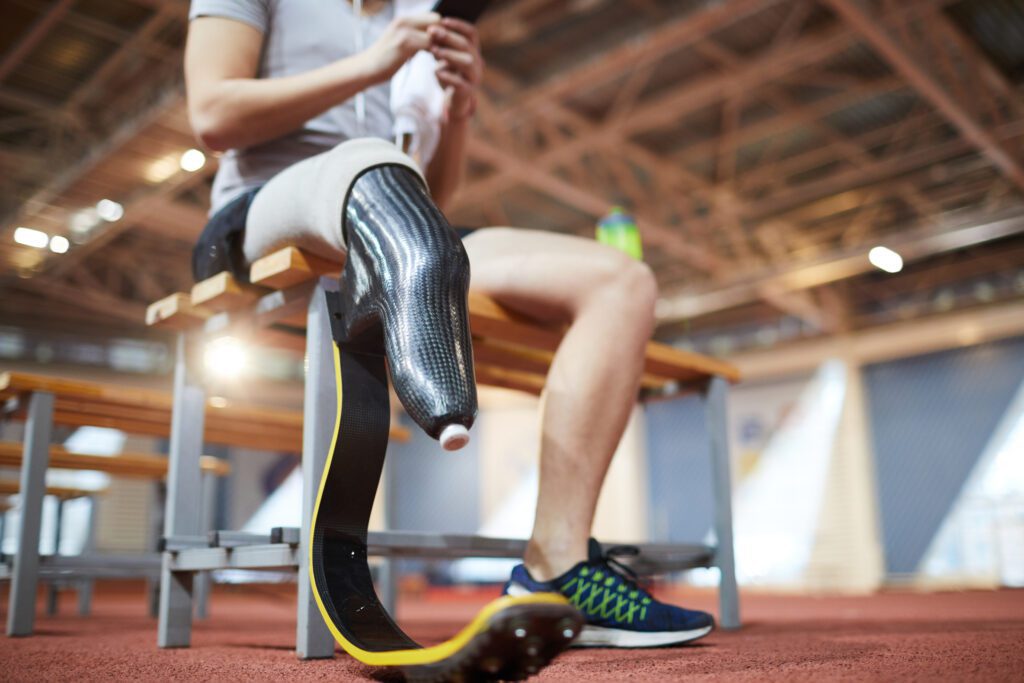
Precision Components for Medical Equipment
Intricate surgical and diagnostic equipment is often manufactured using composite materials, such as medical-grade polymers and titanium alloys, due to their biocompatibility, durability, and lightweight properties. CNC machining enables the production of custom components with tight tolerances and intricate designs, meeting the exact requirements of medical applications, from surgical robots to imaging systems and implantable devices.
Custom Prosthetics and Orthotics Fabrication
Composite materials combined with CNC machining allow prosthetists and orthotic specialists to create bespoke devices tailored to each patient’s unique anatomical needs. From prosthetic limbs to orthotic braces and supports, these custom-fabricated devices offer optimal fit, comfort and functionality. This enables proper alignment and biomechanics support.
Strategic Advancements in Military and Defence
In the military and defence industry, strategic advancements rely on the use of composite materials and CNC machining to enhance performance, durability, and versatility. Several components are manufactured using these technologies, including:
- Aircraft components
- Armoured vehicle parts
- Weapon systems
- Communication and surveillance equipment
- Marine vessel components
The combination of composites and CNC machining enables components to provide accuracy, reliability and protection in combat situations.
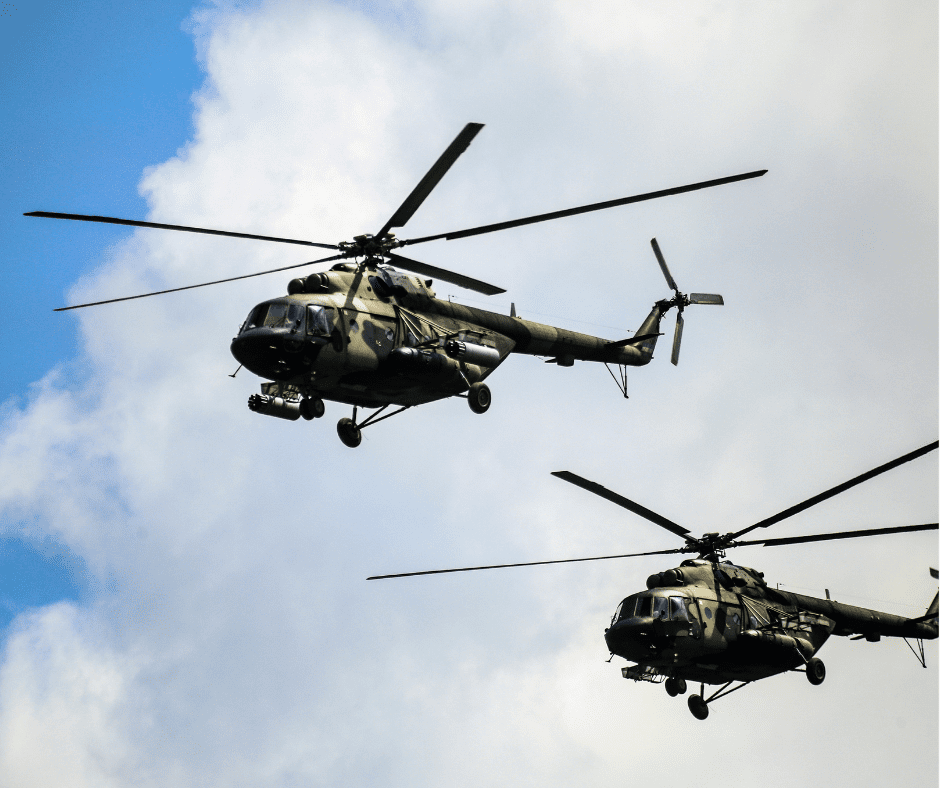
Manufacturing of Critical Defence Components
Composite materials, such as carbon fibre-reinforced polymers (CFRP) and ballistic ceramics, offer lightweight yet robust solutions that enhance mobility and protection in combat scenarios. By using advanced materials and machining techniques, manufacturers can produce critical defence components that withstand the challenges of warfare and enhance operational capabilities.
Prototyping and Testing of Defence Innovations
Defence innovators can rapidly prototype and refine cutting-edge solutions for military challenges using composites and CNC machining. Whether it’s developing next-generation aircraft components, armoured vehicle upgrades, or advanced weapon systems, the use of composite materials allows for lightweight yet robust prototypes that mimic the performance of final products.
Conclusion
Advanced manufacturing processes using CNC machining and composite materials enable high-performance, precision components to be manufactured in a variety of industries. CNC machining supports the manufacture of complex designs with precise dimensions. While composite materials enhance strength-to-weight ratios, durability and aerodynamic efficiency. By combining composite materials with CNC machining, manufacturers can prototype, test, and design high-performance solutions for components in various sectors.
CNC machines suitable for use with composite materials include CNC milling machines, turning machines, router machines, laser cutters, and 3D printing machines.
At Piran Composites we offer CNC services for a variety of industries alongside our complete design, engineering and manufacturing capabilities.
We manufacture top-quality prototypes and large quantities of components for diverse applications, from space exploration to medical devices. With our world-leading facilities and expert team, we can turn any idea or concept into reality.
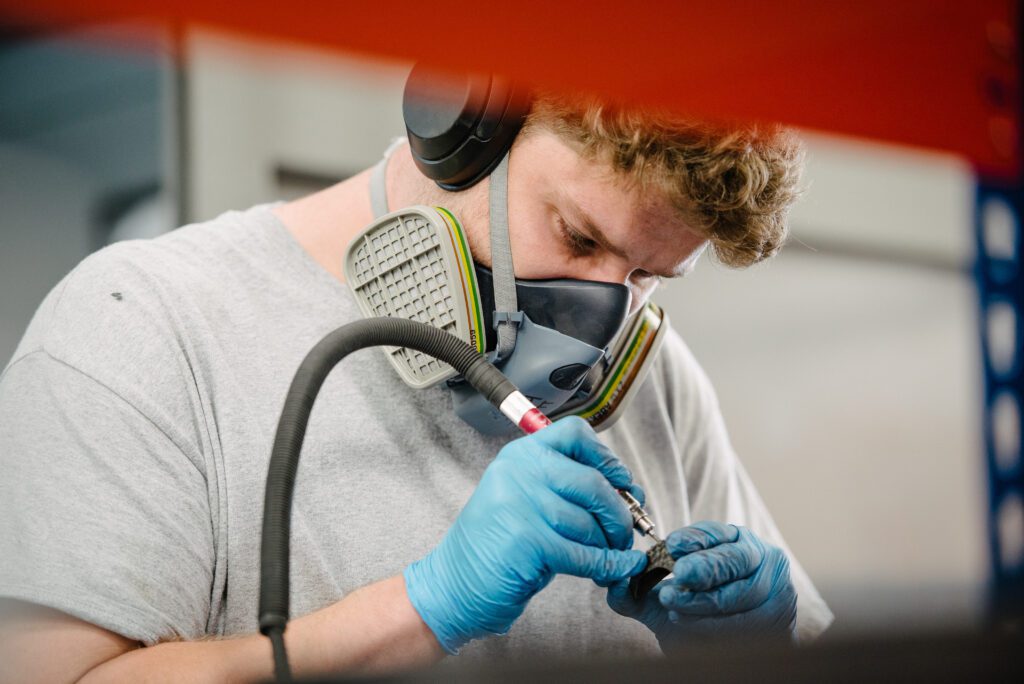