The composite manufacturing process varies according to materials and desired output for the final composite material. The three main composite manufacturing processes are open moulding, closed moulding and cast polymer moulding. Then there are a variety of processing methods within each of these. Which composite manufacturing methods are used is a decision made according to the material, design and application of the final composite.
With growing demand for this durable, robust and lightweight product many industries are turning to the use of composite materials. But a question often asked is “how are composites manufactured?”. Below, we will explain the various methods in a little more detail which should enable you to make a more informed decision when choosing your preferred composite.
Table of Contents
What is Composite Manufacturing?
To put it simply, composite manufacturing is the process required to produce the final composite material. There are a number of techniques available and the chosen composite manufacturing method will always be driven by the final desired output, taking into consideration the materials needed as well as design.
How are Composites Manufactured?
Thanks to advances in composites manufacturing and process design there are a range of ways to manufacture composites. From hand lay-up to filament winding, braiding and weaving to 3D printing, the route to a final composite material which is fit for purpose is often bespoke. This ensures that the finished product matches the specifications for the particular project.
However, two very different techniques can produce what may appear to be the same outcome, which only adds to this already complex process. Below we unpick some of the most commonly used composite manufacturing processes, each of which is very different and suited to an array of finished part sizes and types.
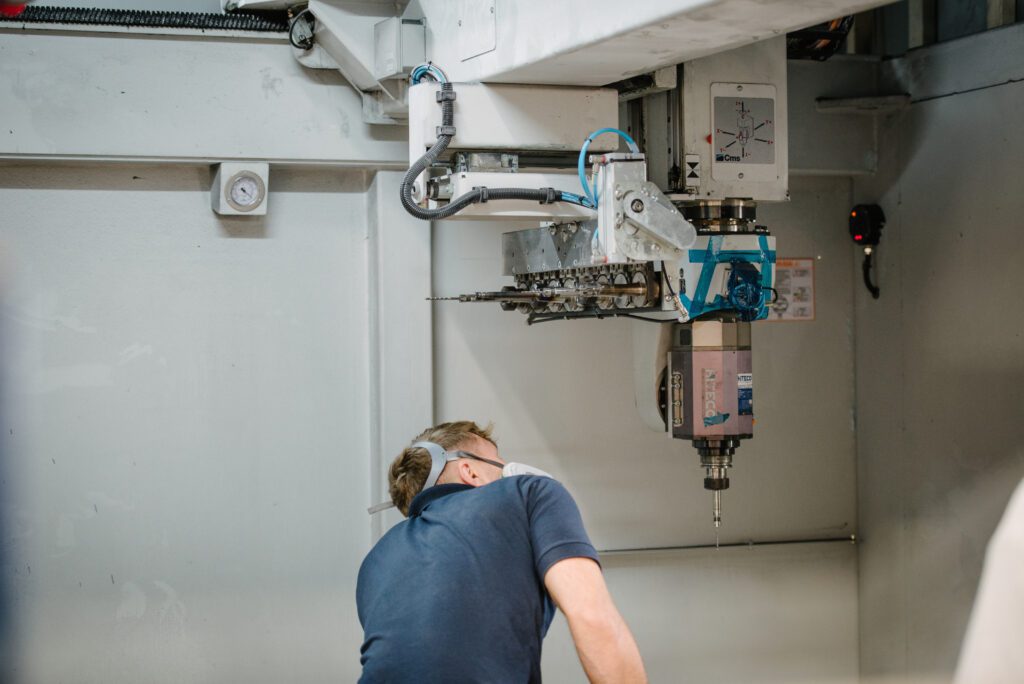
Closed Moulding Composite Manufacturing Process
Closed moulding composite manufacturing processes involve creating parts or products in a closed or sealed mould, providing a controlled environment for the curing or solidification of the composite materials. This process offers advantages like precise material control, higher fibre volume fractions, improved mechanical properties, reduced emissions, and suitability for producing complex parts.
Closed Moulding Composite Manufacturing Methods:
1.PrePeg / Pre-impregnated Fibres
This process is widely used, and is progressively taking the place of conventional metal materials, especially for the aerospace industry. Prepeg, is a composite material manufacturing process that entails the impregnation of reinforcing fibres like carbon, glass or aramid fibres. In the course of composite manufacturing, the prepeg material is carefully positioned within moulds or tools, followed by the precise application of heat and pressure to cure the resin, thereby shaping the desired composite structure and yielding a composite material of superior strength and performance.
The resin pre-impregnation process for the fibres is meticulously conducted within a controlled environment, guaranteeing comprehensive impregnation with the specified resin ratio and distribution. This meticulous approach ensures the attainment of optimal quality and reliability.
2.Resin Transfer Moulding (RTM)
This particular composite manufacturing method sees reactive resin mixed before being injected into the mould under pressure. Similar to infusion moulding but using a pump or pressure pot to force the resin in at a considerably higher pressure. Such injection pressures are often around 10-20 bar(150-300psi) however they can be as high as 100bar (1500psi) in certain high production methods which is a considerable amount of pressure!
This high pressure is then maintained until the resin has cured in the mould which is often bolted or clamped together in a large hydraulic press with flat platens. These ensure the moulds stay aligned during the curing process. RTM is great for complex parts and is a composite manufacturing process used in a wide range of industries such as the automotive sector.
3. Vacuum Infusion
Perfect for boat hulls or wind turbine blades, vacuum infusion is used to create a low viscosity resin which then impregnates a fibrous preform. A stack of dry fibre reinforcement is placed into the mould followed by a vacuum bag with a plumbing system over the top. A vacuum is then pulled which allows the pressure differential between the inside and outside of the bag to push resin into the dry laminate.
This vacuum process forces resin to flow over the surface of the preform, permeating through the thickness which minimises the distance the resin must travel through the preform.
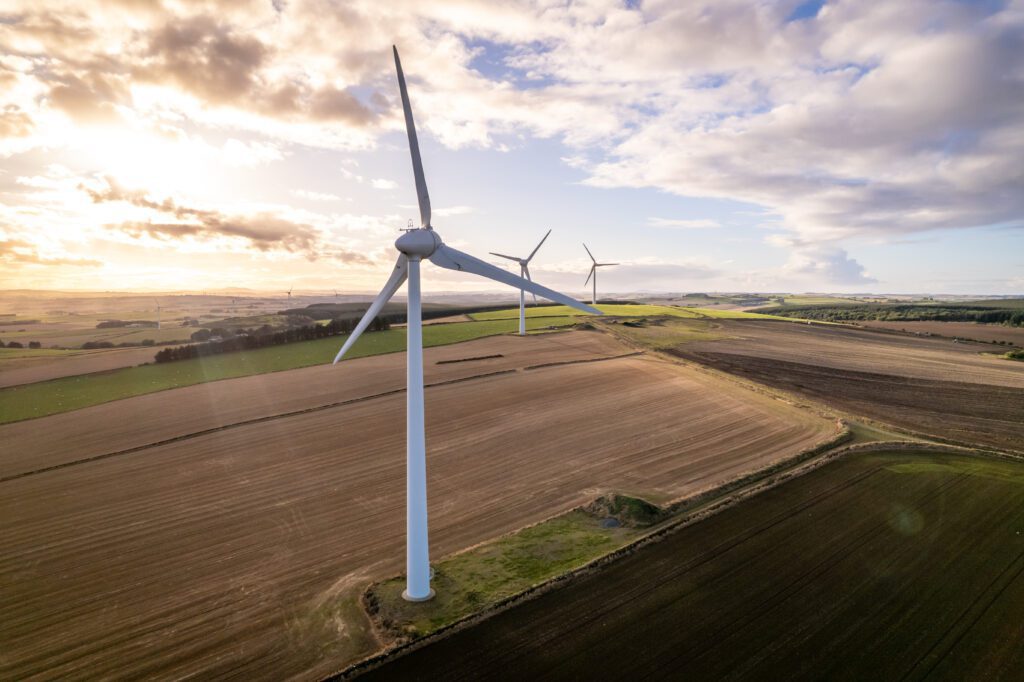
4. Compression Moulding
Ideal for fairly small products needing fully moulded geometry, compression moulding can be done with either thermoset or thermoplastic resins as well as a wide range of different fibre types and lengths. The process itself sees a charge of fibre and resin placed into a preheated mould which is closed and kept under pressure until the resin has cured. A Class A surface finish can be achieved which has seen this composite manufacturing method applied to the automotive industry in particular.
5. Injection Moulding
Injection moulding is arguably the most widely used net-shape manufacturing process for composite materials. Bulk moulding compound is heated before being injected into a heated mould where it is held under pressure until the resin has cured.
Used primarily for fairly small components, injection moulding can mass produce high precision parts requiring specific geometry at a low cost. Such products have been widely used for baby care products to medical devices, electronic appliances and in aviation. As advances are made in the composites manufacturing and design process, more and more materials are being used in injection moulding to meet the increasing demand for varying plastic products.
6. Autoclave Curing
This is a closed moulding composite manufacturing tool which uses pressurised steam to perform a range of processes. By creating a high pressure environment inside the autoclave, it is possible to produce accurate results with the desired fibre content. The process itself involved curing raw materials inside a two sided mould or, in some instances, a deoxygenated vacuum bag. Both processes are able to produce large quantities of material which makes this a highly suitable process for large facilities.
Autoclave curing guarantees consistent polymer hardening which makes it excellent for manufacturing composites. After applying a release gel on to the moulds surface, fibre textiles are placed into the mould, these are prepregs so have already been saturated with resin.
Once the moulds are full the air is vacuumed out of the cavity and the entire assembly is placed into the vacuum bag. After all the air has been removed from the bag the container is placed into the autoclave for the curing process to begin. The temperature and pressure are increased slowly whilst curing which hardens the material whilst removing pores. From here the product is transferred into an oven where its durability will be further enhanced.
With a good degree of uniformity the autoclaving composite manufacturing process is often used to produce high strength to ratio parts. Such as would be used in aircraft components as well as for the military, marine industry, space crafts and missiles.
7. Braiding and Weaving
Last on our list but certainly not least, braiding and weaving are narrow width textile composite manufacturing methods. Braiding is used in a host of end products including garments, shoes, ropes and cables. It is a highly suitable method for developing seamless cylindrical textile reinforcement for developing composite structures and as a fast manufacturing process with reduced wastage, it is the perfect composite manufacturing process for numerous items.
Incredibly strong braided composites are known for their superior toughness and durability, particularly when compared to filament wound composites. They are used in a variety of applications from aerospace to prosthetics and a range of braided fabrics can be created with a number of configurations using carbon, glass, aramid and hybrid fibre systems.
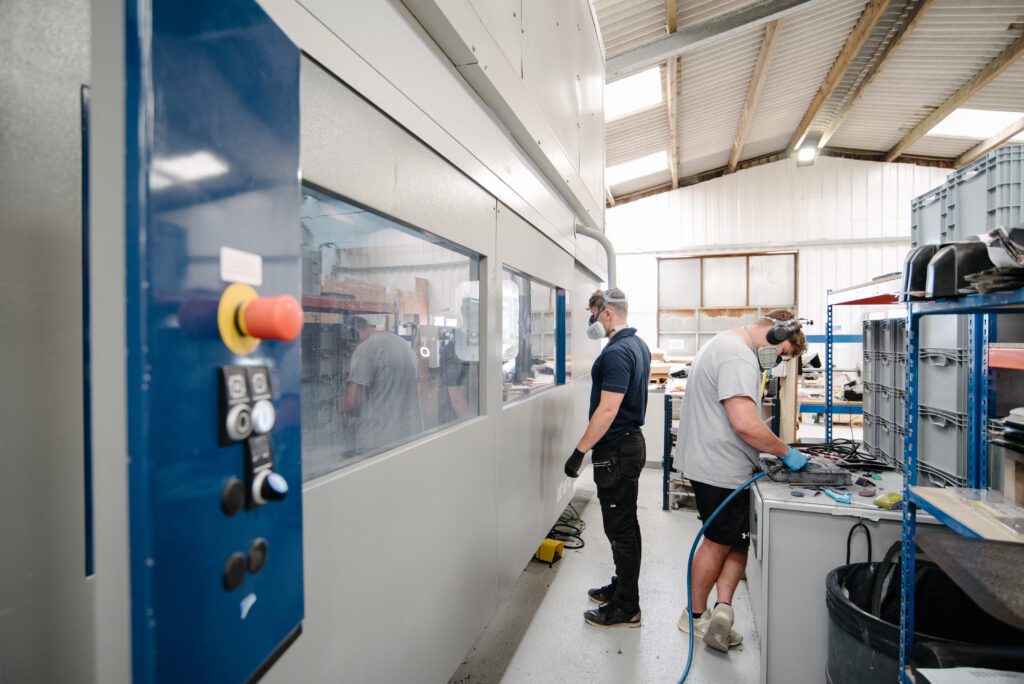
Open Moulding Composite Manufacturing Process
Open moulding composite manufacturing processes involve creating composite parts in an open mould, allowing for easy access to the mould and direct application of composite materials. Unlike closed moulding processes where the mould is sealed, open moulding processes are more straightforward and typically result in parts with less precise control over material distribution. This manufacturing process is often used for production parts with lower tooling costs, faster production times, and simplicity in design.
Open Moulding Composite Manufacturing Methods:
1.Hand Lay-Up
This composite manufacturing method sees fibres meticulously positioned on or into the mould before being wetted with liquid resin. This is manually applied by our experienced laminator before it is rolled out and left to cure or vacuum bagged. The fibres used in this process can be of any material as long as it is in the form of chopped strand mat, woven, knitted, stitched or bonded fabrics.
As you can imagine, hand lay up requires incredible attention to detail with the laminating features needing to be achieved before the resin starts to cure. This is a naturally time limiting and highly pressured role which can place restrictions on the amount of detailing and tailoring that is possible.
As an overview, hand lay up (or wet lay up) can be a cost effective manufacturing process for composite materials requiring a chopper gun and roller. Or it can be highly specialist and more expensive using vacuum bags and epoxy. If you would like to understand these in more detail just give our knowledgeable team a call to talk through your options.
2. Spray-Up
Unsurprisingly, this composite manufacturing process uses a spray gun to apply a mixture of resin and short strands of fibreglass to a mould until the desired material depth is achieved. In the hands of our skilled operators, these spray up guns are able to laminate speedily and neatly, providing the operator pays attention to detail during the spraying and rolling process. After spraying the resin is cured before being ready to use.
Whilst this is a fast and cost-effective composite manufacturing process, the mechanical properties are often lower and not advised for high performance. The finished composite product is generally resin rich with variable thickness which can be hard to control. It is an advisable process for large, fairly simple structures such as boat hulls, bath tubs and storage tanks.
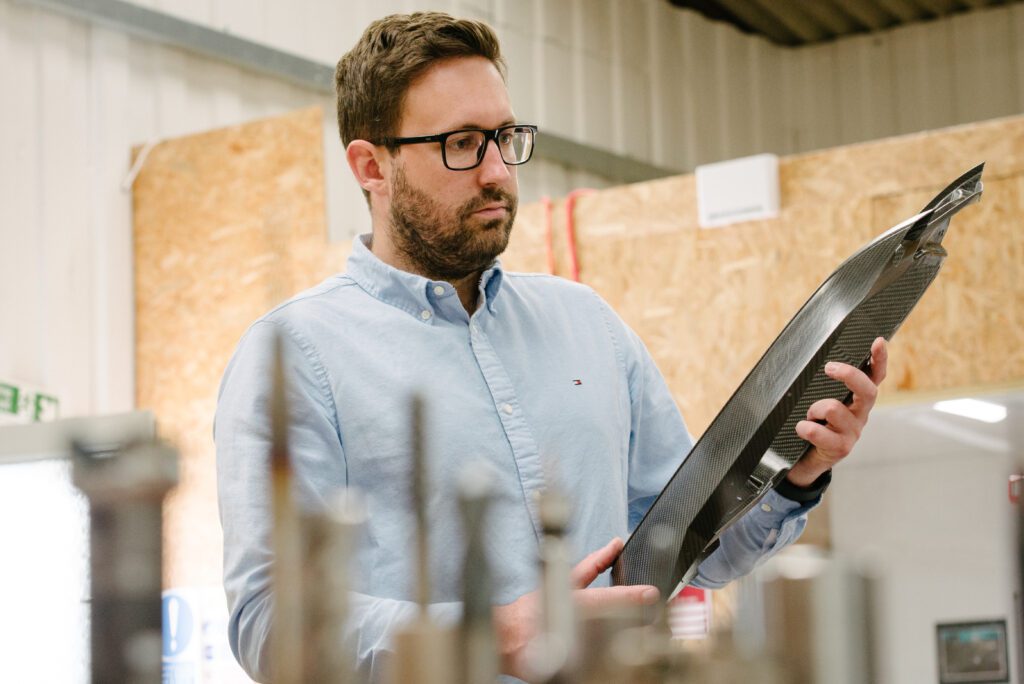
3. Filament Winding
This well developed and renown industrial process is recommended for a select band of composite products. Filament winding requires the use of a mandrel, often a slim, long male mould. This part is made by passing a fibre tow through a resin bath from where it is applied under tension to the mandrel.
To control the direction and angle of this wrapping, we use a carriage with a winding guide which is moved up and down the mandrel’s length whilst the mandrel itself is rotated. Using this synchronised movement enables the fibre to be laid at a specific angle to achieve the required geometry. This is then left to cure under heightened temperatures if needed.
For higher volume production needs this composite manufacturing process can easily be automated and is often used for tubular items or products with a simply revolved shape. This can include pipes, pressure tanks, tapered poles and drive shafts along with specialist items including high performance items such as bicycle frames. These generally use a combination of carbon fibre and epoxy with a mandrel wrapped prepreg to result in a much lighter, stronger tubular structure.
Whilst this may be a more expensive carbon fibre composite manufacturing process it is our recommended option for thicker and more highly engineered tubular shapes.
4.Pultrusion
In this manufacturing process of composite materials, wet fibre tows are fed through a heated, shaped extrusion die. The fibre and resin goes in as one before being pulled out as a fully cured part. As you can probably imagine, such a process results in a long item with a consistent sectional shape, axial reinforcement and consistent cross section. Produced with high accuracy, pultrusion is a great composite manufacturing process for ladder sections, bridge parts and handrails to name a few. The process can easily be automated whilst using low-cost raw materials which makes it perfect for high volume outputs.
5. 3D Printing/ Additive Manufacturing
Widely regarded as an innovation which has transformed composite manufacturing processes, 3D printing or additive manufacturing is disrupting the industry – in a good way!
This composite manufacturing method uses 3D printing to produce functional components such as tools and end-use production parts. Additive manufacturing builds geometries by weaving in feedstock such as filament, wires or powder. Then, according to the 3D printing process and application, additive manufacturing can draw on an ever-growing catalogue of materials and is arguably the most general category of manufacturing around.
Initially popular in the aerospace and medical industries, additive manufacturing is completely flexible, easily applied to a host of end markets including dental, automotive, oil, gas, heavy equipment and consumer goods. When compared to subtractive processes such as milling, additive manufacturing allows for greater geometric freedoms whilst using less materials. Plus 3D printing doesn’t require any moulds or tooling to create parts, lending itself as a great option for applications where long lead times or associated costs have.
Summary
To summaries the list of different composite manufacturing processes, methods and techniques, Piran Advanced Composites specialise in using a vast number of different techniques when processing and manufacturing advanced composite materials. By leveraging our extensive knowledge, we handle pre-impregnated carbon, glass and aramid fibres, in addition to epoxy, cyanate ester, and phenolic resin systems, that fulfil the demanding criteria of durability, weight, and temperatures across various applications.
To learn more about Piran Advanced Composites and our manufacturing processes please contact our team today.
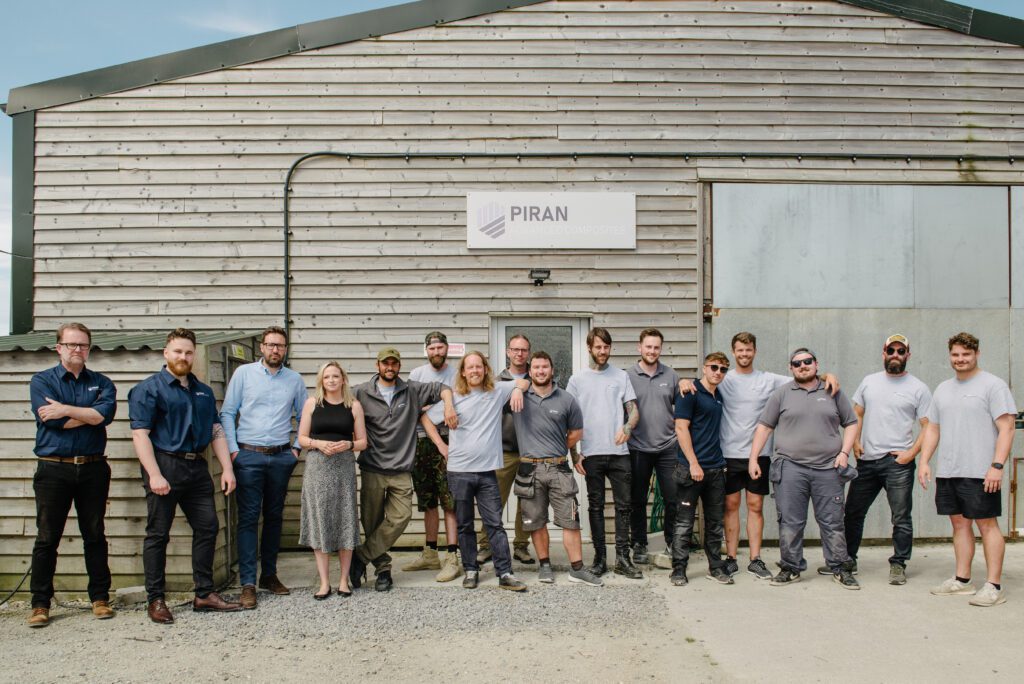