In this article, we embark on an insightful exploration of fibreglass composites, delving into the intricate properties and sophisticated manufacturing processes that underpin this pivotal material in contemporary engineering and design. Fibreglass composites, renowned for their exceptional strength-to-weight ratio and adaptability, play a crucial role across a spectrum of industries, ranging from aerospace engineering to the production of sports equipment.
Table of Contents
What is Fibreglass?
Fibreglass, also known as glass fibre, is a material consisting of numerous extremely fine fibres of glass. It is made by forcing molten glass through a sieve that spins it into threads, which are then combined to form fibreglass.
This material is known for its strength, durability, and lightweight properties. It’s non-conductive, non-flammable, and can be moulded into various shapes, making it versatile for different applications.
Fibreglass is used in a wide range of industries, including automotive, construction, and telecommunications. Its unique properties arise from the combination of glass itself, which is durable and weather-resistant, with the structure of the fibres, which adds strength while remaining flexible.
What is Fibreglass Composite?
Fibreglass composites are a reinforced plastic material composed of glass fibre embedded in a resin matrix. This combination results in a material that surpasses the properties of each individual component.
The glass fibres provide strength and stiffness, while the resin matrix binds the fibres together and distributes stresses evenly throughout the material. The term “composite” refers to the combination of two or more distinct materials to create a new material with enhanced properties.
This material is notable for its high strength-to-weight ratio, corrosion resistance, and thermal conductivity. It is widely used in industries such as aerospace, marine, automotive, and sports equipment manufacturing. The versatility of this material allows for a broad range of applications, from simple household items to complex structural components in high-tech fields.
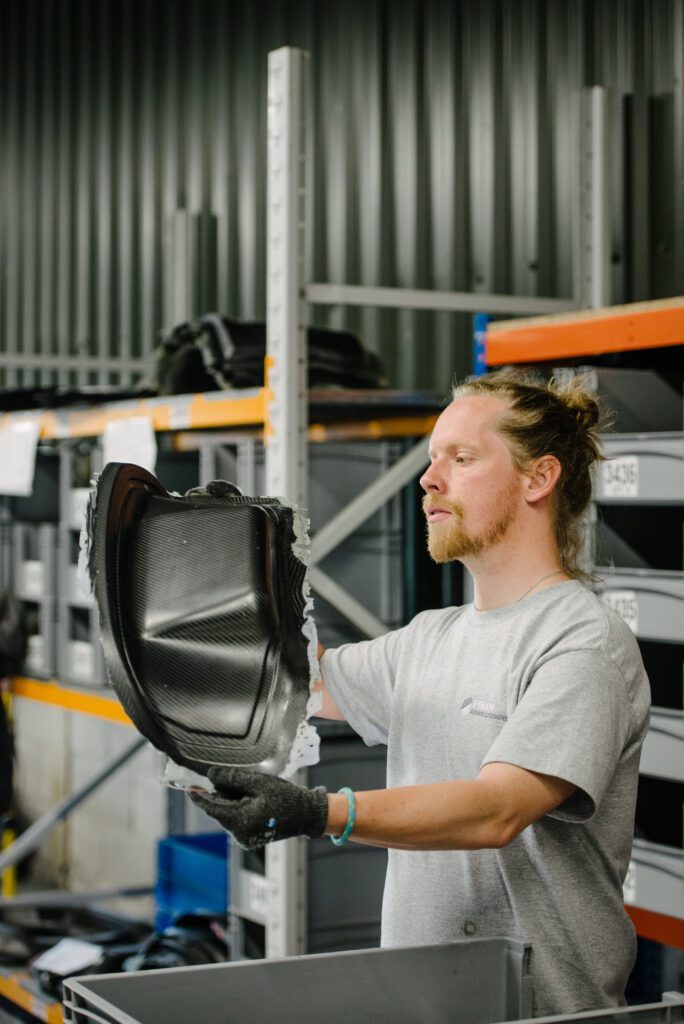
History of Fibreglass Composite
The history of fibreglass composite traces back to the late 1930s, when researchers began experimenting with glass fibres to reinforce plastic materials. The initial discovery of glass fibre reinforced plastic was made almost by accident. In 1935, a researcher named Games Slayter, working for Owens-Illinois Glass Company, directed a jet of compressed air at a stream of molten glass, resulting in the creation of fine glass fibres. This marked the birth of fibreglass.
During World War II, the development of composite materials received a significant boost as there was a need for lightweight and strong materials for military applications. Fibreglass began to be used in radomes (protective covers for radar) and aircraft components. The war era also witnessed the development of epoxy and polyester resins, which played a crucial role in the advancement of fibreglass composites.
Post-war, the use of the material expanded rapidly into commercial markets. The 1950s and 1960s saw a significant increase in the use of fibreglass in boats, cars, and construction materials. The material’s ability to be moulded into complex shapes made it ideal for these applications.
The 1970s and 1980s marked further technological advancements in the manufacturing processes and the quality of fibreglass composite. Innovations in fibre weaving and resin chemistry allowed for the creation of stronger and more durable composites. These developments opened up new opportunities in various industries, including aerospace, where composite fibreglass began to be used more extensively due to its strength and lightweight properties.
In recent decades, the evolution of fibreglass composite has continued, with a focus on enhancing its strength, reducing its weight, and improving its environmental sustainability.
Today, it’s a critical material in numerous industries, renowned for its versatility and advanced properties that have been refined over decades of research and development.
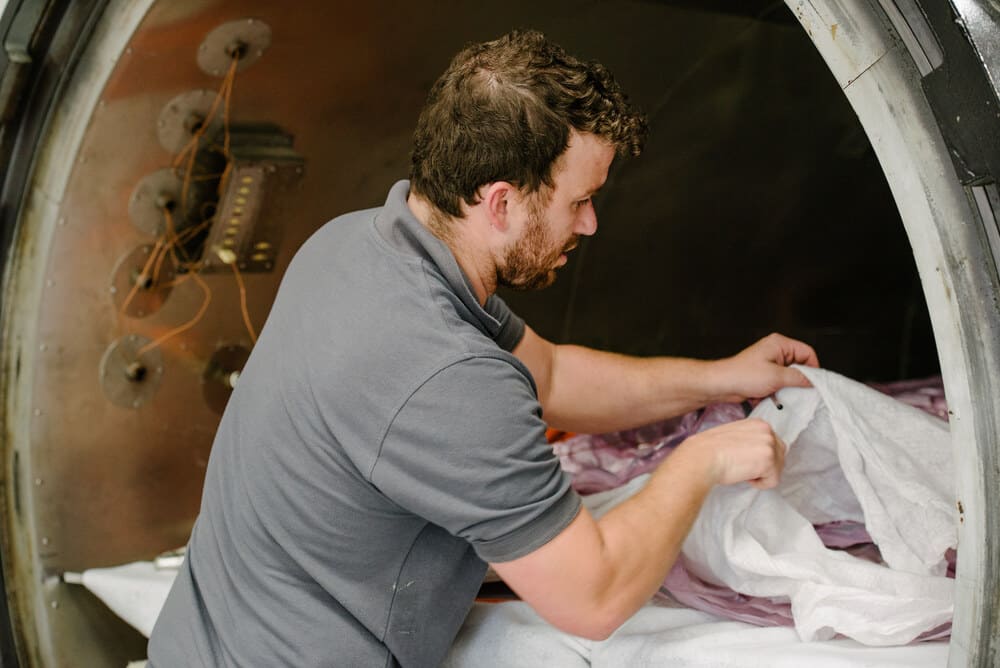
Manufacturing Process of Fibreglass Composite
The manufacturing process of fibreglass composite is intricate, involving several key steps to create a material that is both strong and lightweight. Here’s a detailed look at each step in the process:
Step 1: Making of Fibreglass Strands
This first step involves the production of fibreglass strands. Raw materials like silica sand, limestone, and various chemical additives are melted together at high temperatures to form molten glass.
This molten glass is then extruded through fine nozzles to create thin strands of glass fibres. These strands can be woven into fabrics or mats, or used as they are, depending on the intended application.
Step 2: Impregnating Fibres with Resin
Once the fibreglass strands are ready, they are impregnated with a resin mixture. This resin acts as a binding agent and provides the composite material with its shape and additional properties like chemical resistance and strength.
The type of resin used can vary, with common choices being polyester, epoxy, or vinyl ester, each offering different characteristics to the final product.
Step 3: Moulding and Shaping
In this stage, the resin-impregnated fibres are moulded into the desired shape. This can be done through various techniques such as hand lay-up, where the fibres are manually placed in a mould, or through more automated processes like pultrusion or filament winding.
The choice of method depends on the complexity of the design and the required strength of the final product.
Step 4: Curing and Finishing
The final step is curing, where the moulded material is subjected to heat and pressure to harden and set the resin, thus solidifying the composite structure.
After curing, the fibreglass composite can undergo various finishing processes, including trimming, painting, or polishing to meet specific aesthetic or functional requirements. This step solidifies the composite’s structural integrity and finalises its properties.
Each of these steps is critical in the manufacturing of fibreglass composite, ensuring the material’s high performance in various applications ranging from automotive parts to aerospace components.
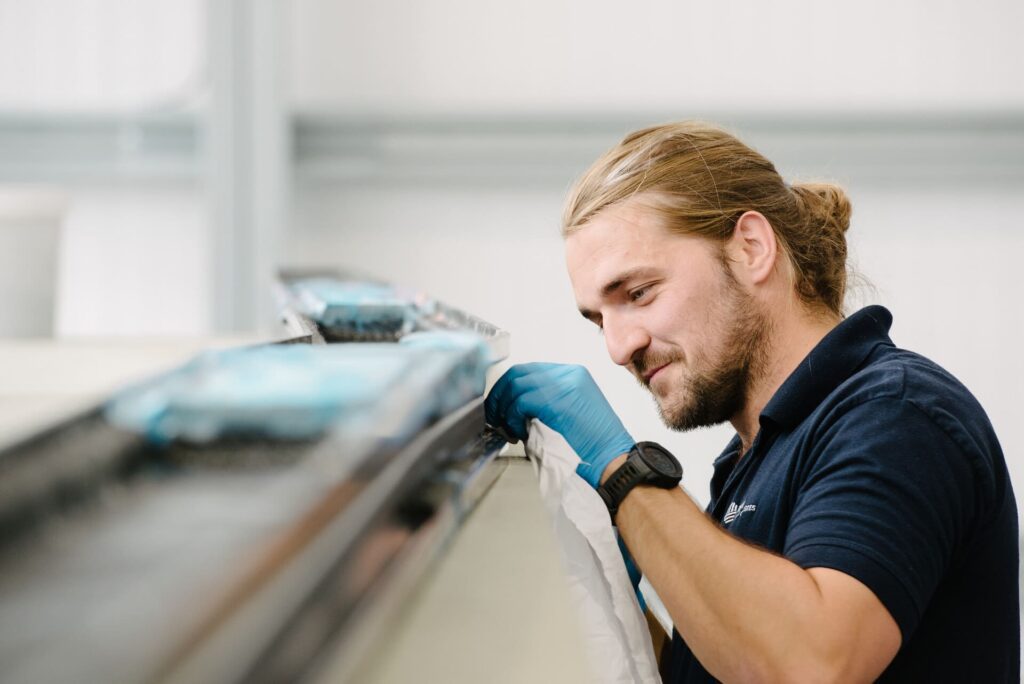
Applications of Fibreglass Composite
Below, we explore its diverse applications, particularly in the automotive, aerospace, marine engineering, construction, and sports equipment sectors.
Automotive Industry
In the automotive industry, fibreglass composite is used for its lightweight and strong characteristics, enhancing vehicle performance and efficiency. It is employed in manufacturing car components such as bumpers, body panels, and dashboards.
This material’s impact absorption capabilities improve vehicle safety, and its thermal insulation properties are crucial in engine compartments. Additionally, its resistance to corrosion extends the lifespan of vehicle parts, especially in harsh environments.
The design flexibility offered by fibreglass composites enables the creation of aerodynamic and aesthetically pleasing vehicle designs, making it particularly popular in high-performance and luxury vehicles.
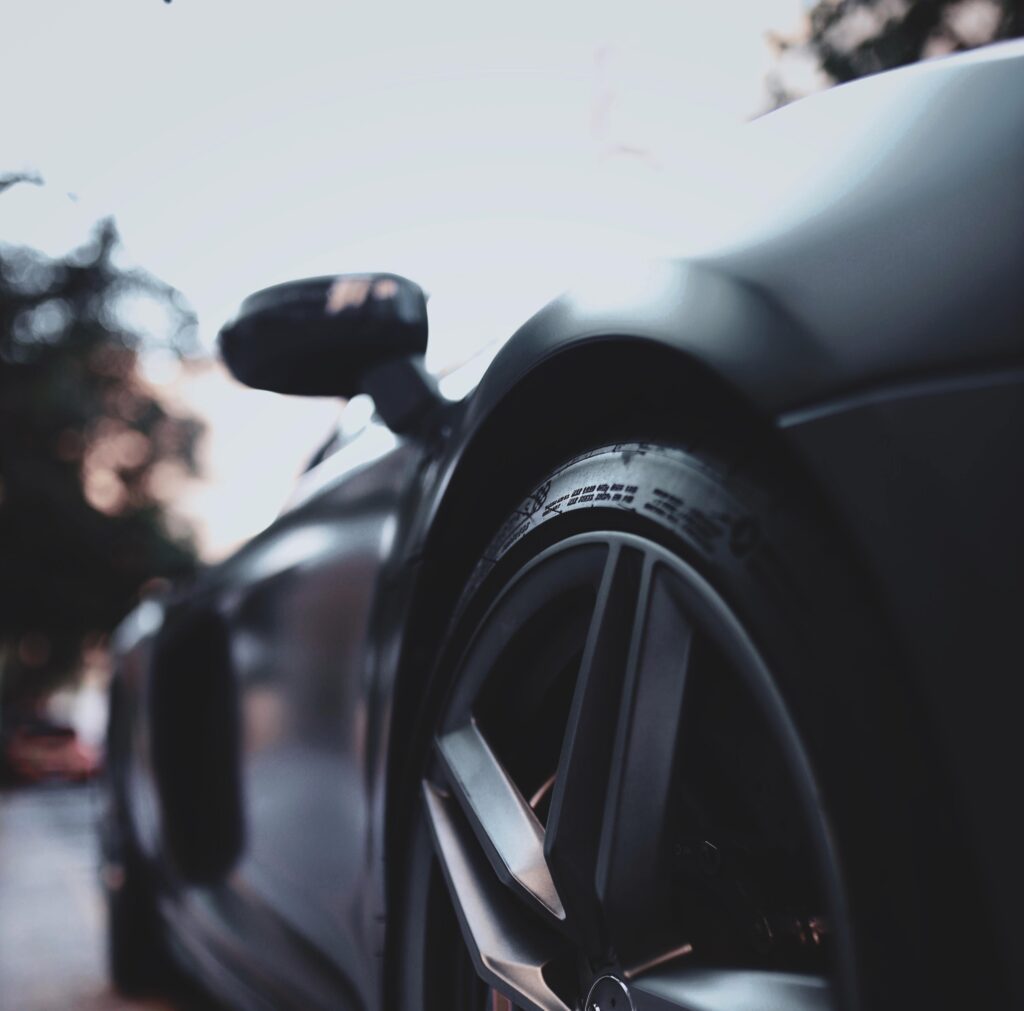
Aerospace and Marine Engineering
In aerospace and marine engineering, fibreglass composite is highly valued for its resilience, light weight, and resistance to harsh environmental conditions.
Aerospace applications include parts of aircraft bodies, interior cabin components, and insulation panels, where the material’s lightweight nature contributes to fuel efficiency and overall performance.
In marine engineering, fibreglass composites are used in boat hulls, decks, and masts due to their resistance to water and salt corrosion, as well as their ability to withstand the stresses of marine environments. These properties significantly enhance the durability and safety of both aircraft and marine vessels.
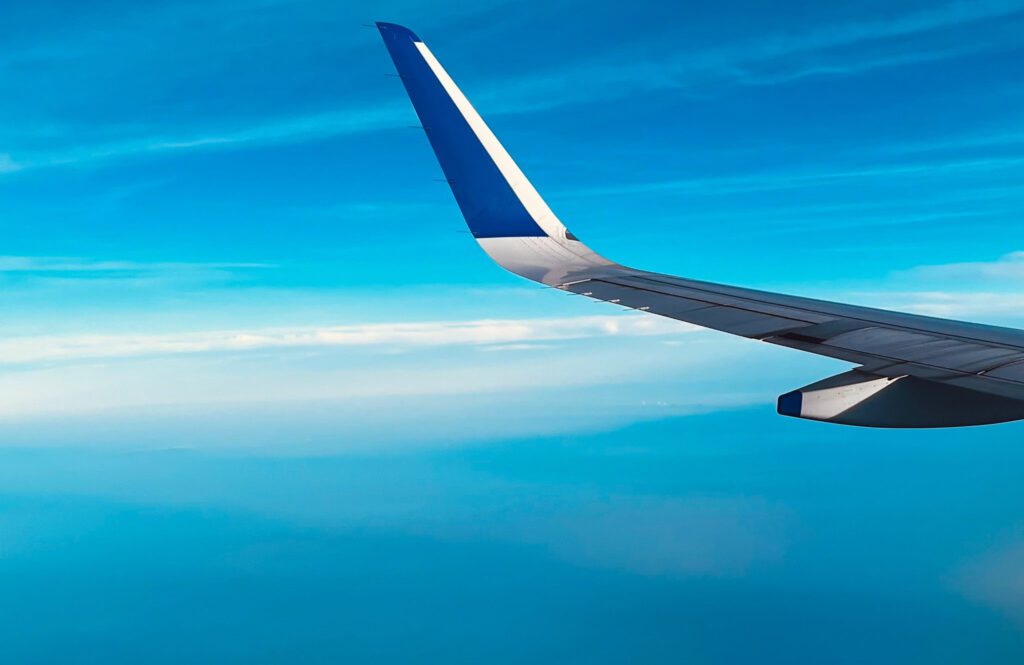
Construction and Sports Equipment
In the construction industry, fibreglass composite is utilised for its strength, flexibility, and resistance to environmental wear. It’s used in roofing, piping, and as reinforcement material in concrete. The material’s insulation properties also make it ideal for thermal and acoustic applications.
In the world of sports equipment, fibreglass composites are prevalent in the manufacturing of items like skis, hockey sticks, bicycles, and racing car components. The material’s ability to be moulded into complex shapes and its combination of lightness and strength make it perfect for high-performance sports gear that demands both durability and agility.
These applications of fibreglass composite across diverse sectors underscore its importance as a multifaceted and highly functional material in modern manufacturing and engineering.
Advantages of Fibreglass Composite
Fibreglass composite is celebrated for its numerous advantages, making it a preferred material in a wide range of applications. Below, we delve into some of its key benefits, including its impressive strength-to-weight ratio, corrosion resistance and durability, and versatility in applications.
Strength-to-Weight Ratio
One of the most significant advantages of fibreglass composite is its exceptional strength-to-weight ratio. This means it provides high strength while being remarkably lightweight.
This quality is crucial in industries like aerospace and automotive, where reducing the weight of components can lead to increased fuel efficiency and better performance.
The lightweight nature of fibreglass composites also makes them easier to handle and install, which is particularly beneficial in construction and manufacturing sectors.
Corrosion Resistance and Durability
Fibreglass composite is highly resistant to corrosion, making it an ideal material for use in harsh or corrosive environments, such as marine and chemical processing industries.
Unlike metals, it does not rust or corrode when exposed to water, chemicals, or salt air. This resistance extends the lifespan of products made from fibreglass composite, reducing maintenance costs and the need for frequent replacements.
Additionally, fibreglass composites are known for their durability and ability to withstand wear and tear, making them suitable for heavy-duty applications.
Versatility in Applications
The versatility of fibreglass composite is another one of its standout advantages. It can be moulded into almost any shape and size, which allows for its use in a vast array of products, from boat hulls and car bodies to wind turbine blades and sports equipment.
This moldability, combined with its other properties like strength and corrosion resistance, means that it can be tailored to meet specific needs across different industries.
Furthermore, fibreglass composite can be engineered to possess additional properties such as increased fire resistance or electrical conductivity, broadening its range of applications even further.
The combination of these advantages makes fibreglass composite a highly valuable and versatile material in modern engineering and manufacturing, offering solutions to a myriad of design and functionality challenges.
Challenges and Limitations
While fibreglass composite offers numerous advantages, there are also challenges and limitations associated with its use. Understanding these factors is crucial for industries that rely on this material.
Here’s an insight into the key challenges, including environmental impact, manufacturing complexities, and cost considerations.
Environmental Impact and Recycling Issues
One of the significant challenges associated with fibreglass composite is its environmental impact. The production process can be energy-intensive and may involve the use of chemicals that are harmful to the environment.
Additionally, at the end of its life cycle, fibreglass composite can be difficult to recycle due to the resin matrix that holds the fibres together. This leads to challenges in disposing of fibreglass products, as they often end up in landfills where they do not decompose easily.
Efforts are being made to develop more sustainable resins and recycling methods, but these challenges remain a significant concern for the industry.

Manufacturing Complexities
The manufacturing process of fibreglass composite is complex and requires precise control over various factors such as temperature, resin composition, and fibre alignment. This complexity can lead to inconsistencies in quality if not carefully managed.
Additionally, the manufacturing process can be time-consuming and requires skilled labour, particularly for complex shapes or high-quality finishes. These factors can limit the speed of production and affect the scalability of using fibreglass composite in certain applications.
Cost Considerations
Another limitation of fibreglass composite is the cost. The materials used, such as high-quality resins and fibreglass strands, can be expensive. Additionally, the complex manufacturing process, which often requires specialised equipment and skilled labour, adds to the overall cost.
While the benefits of using fibreglass composite, such as durability and lightweight properties, can offset these costs in the long run, the initial investment can be a barrier for smaller companies or for applications where cost is a critical factor.
In conclusion, while fibreglass composite is an incredibly versatile and valuable material, it is important to consider these challenges and limitations when deciding to use it in various applications.
Balancing its advantages against these factors is key to making informed decisions in material selection and product design.
The Future of Fibreglass Composites
Fibreglass composite, already a revolutionary material in various industries, is poised for further advancements and expanded applications in the future. This section explores the emerging trends and potential future uses of this versatile material.
Emerging Trends and Technological Advancements
The future of fibreglass composite is marked by significant technological advancements and emerging trends. One key area of development is in the creation of more environmentally friendly resins and sustainable manufacturing processes.
Efforts are underway to develop bio-based resins and more energy-efficient production techniques, reducing the environmental footprint of fibreglass composites.
Another trend is the enhancement of the material’s properties through nanotechnology. By incorporating nanomaterials, researchers are improving the strength, durability, and thermal resistance of fibreglass composite, opening up new possibilities for its application.
Additionally, advancements in 3D printing technology are set to revolutionise the way fibreglass composite is moulded and used, allowing for even more complex shapes and designs with reduced waste and production times.
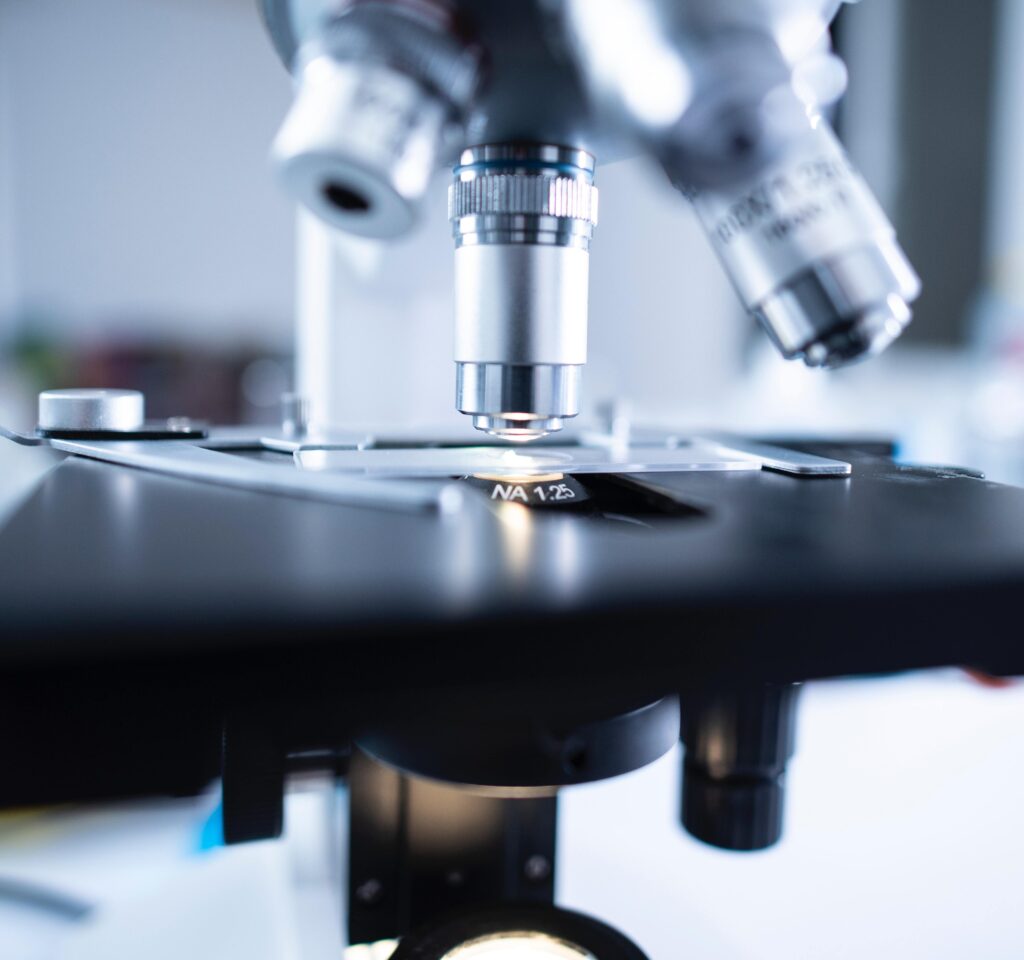
Potential Future Applications
As for future applications, the potential of fibreglass composite is vast. One area of significant growth is in renewable energy, particularly in the construction of wind turbine blades. The material’s strength and lightness make it ideal for creating larger, more efficient turbine blades.
In aerospace, the continued push for lighter and stronger materials suggests an increased reliance on fibreglass composite, potentially in more structural components of aircraft.
Additionally, the automotive industry may see a greater adoption of fibreglass composite in electric vehicles (EVs) to offset the weight of batteries and improve efficiency.
In the field of infrastructure, there’s potential for more extensive use of fibreglass composites in bridge construction and repair, offering a durable, lightweight, and maintenance-free alternative to traditional materials.
In conclusion, the future of fibreglass composite holds exciting prospects, with ongoing innovations and potential applications set to further cement its role as a material of choice in modern engineering and design
Conclusion
As we have explored, fibreglass composite stands as a material of remarkable versatility and strength, offering significant advantages across a wide range of industries.
From the automotive and aerospace sectors to construction and renewable energy, its impact is profound and far-reaching. The future of fibreglass composite is bright, with technological advancements continuously enhancing its properties and expanding its applications.
It offers a solution to many modern engineering challenges, combining strength, flexibility, and durability in a way few other materials can.
We, at Piran Composites are dedicated to leading the charge in harnessing the power of fibreglass composite. Our expertise and commitment to innovation place us at the cutting edge of this exciting field.
Contact us today to learn more about how our fibreglass composite solutions can revolutionise your products and projects. Let’s build the future together with strength, innovation, and sustainability at the core.
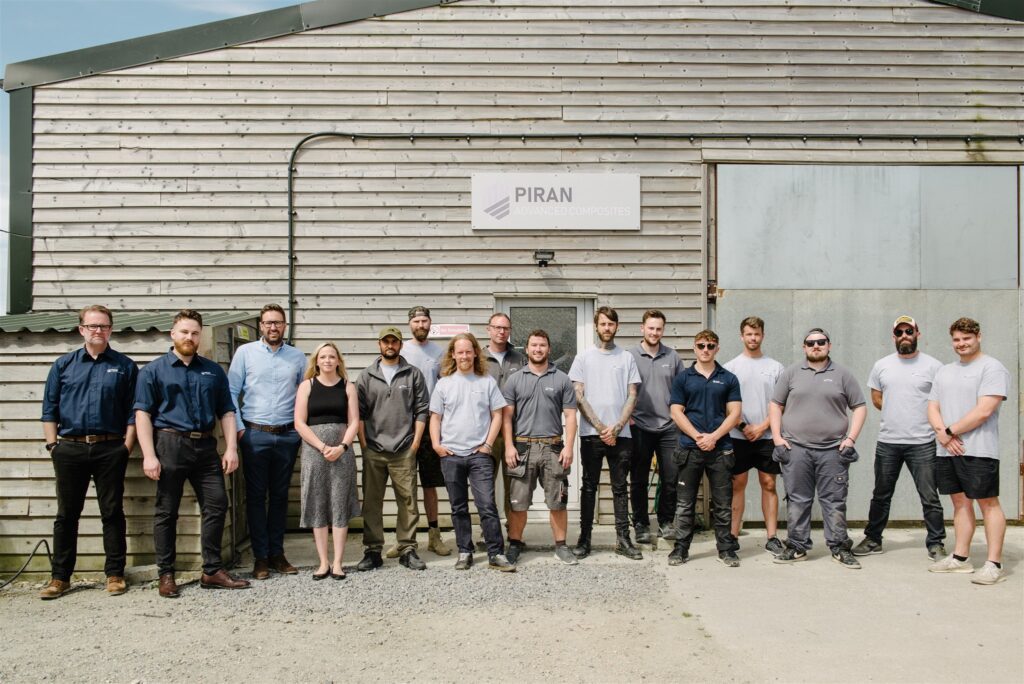